There are 2 main sources of drill solids
particles are the chemical additives and formal drilling cuttings, the drilling
cuttings are containments that degrade the performance of drilling mud. The
drilling particles will be ground into smaller and smaller and become more and
more difficult to remove from drilling mud if the drilling cuttings that not removed as per guide. Most of the
formal drill solids will be able to be removed by mechanical ways by drill
solids separate equipment and small drill particle will be very difficult to
remove and will have a great effect on drilling mud properties than the very
larger drill solids particles . The solids particle size in drilling mud
incorporated into drill mud will be range from 1 to 250 microns.
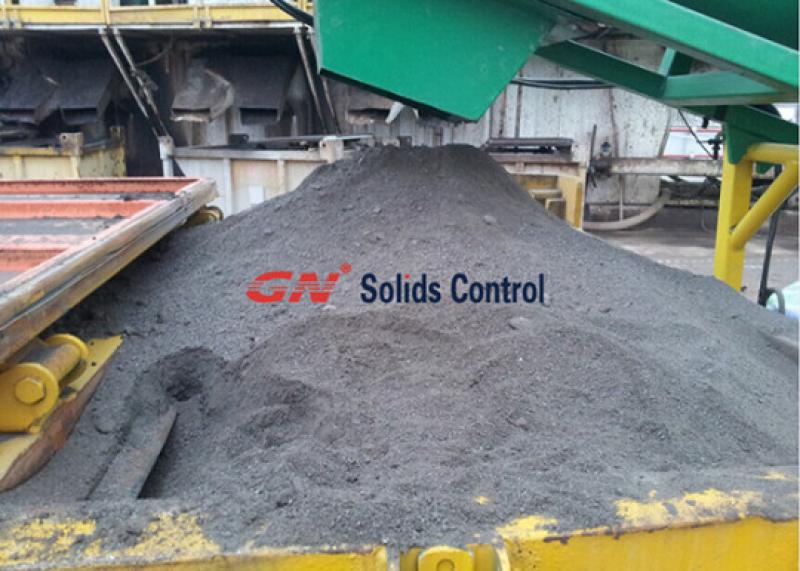
The clay, colloidal and bentonizte will be
size between 1 to 5 microns, silt, barites and fine cement dust will be 6 to 44
microns, fine sand will be between 44 to 74 microns, API sand will be 105 to
149 microns, coarse sand can be 500 – 1000 microns, coarse that larger than
2000 microns, there will be colloidal that bellow 2 microns.
Drilling solids particles are the main contaminant
in the drilling mud, so the control of the importance of the good solids
control including increased the penetration rate and reduce mud cost, reduce
water requirement, reduce mixing problem, reduce differential striking, etc.
The drilling solids removal is important to keep drilling mud recycling and re-use.
The
main equipment for drill solids removal are shale shaker , desander, desilter, decanter centrifuge and there will be other
machine assistant to meet separation application including mud tank, centrifugal pump, valve and pipeline.